Air box detail
#1

Interesting YT air flow demo video
Now take a look at the inside of your air box at the spigot entrance...SHARP CORNERS!
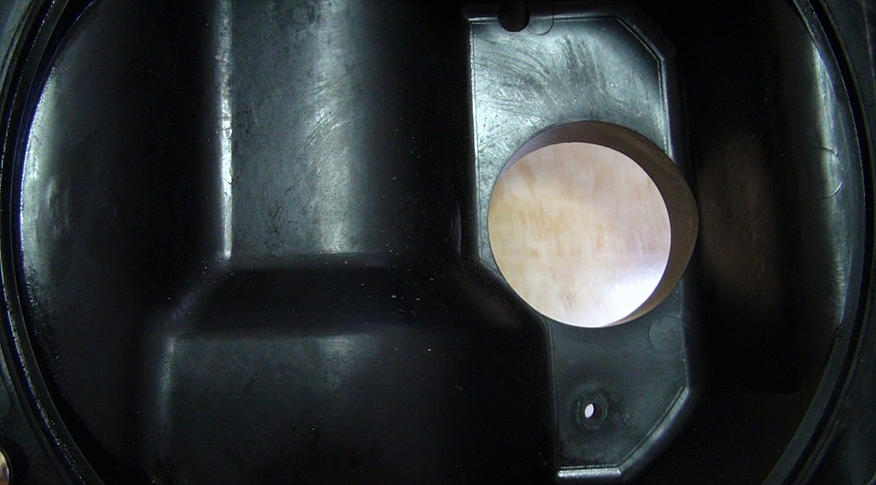
The KLX250 air box is quite different from the previous generation's air box/boot configuration, with it's large-mouthed flange connection to the air box and larger connecting tube to the carb. Maybe that's where some of the KLX300s extra HP came from

I don't think it's possible to retrofit a KLX300 air box to a 2006 and up bike, but some mods can be made to the sharp cornered entrance way. Too bad, it'd be an interesting comparo.
If I was in the US I'd order a proper sized short velocity stack and afix it to the inside of the air box after removing most of one side of the stack. But from this distance it's too much trouble.
The least I'll do is attach a plate with a nice full radius blending up to the edge of the spigot hole in the flat areas above and below the spigot. Flow bench operators make do with just using a plate with rounded corners (1" radius recommended) attached to cylinder head intake ports so that seems to be the quickest and easiest fix. As does the air filter in the YT AEM video above.
Just take off the rubber boot and put something the same size OD as the spigot ID in there to locate the plate as the JB Weld is setting up and it'd be a quick installation.
Every little bit helps
I did read where a guy made velocity stacks for some other bike out of thin walled plastic plumbing by dipping it into boiling water and forcing it over an upside down shower faucet backing plate or something like that. I can buy 10' of the PVC whatever it is that's the same ID as the spigot for $4, and make a mold out of plaster that has a big fat round curve in it. Then force the hot plastic pipe onto the mold's curves and see what happens.
Now take a look at the inside of your air box at the spigot entrance...SHARP CORNERS!
The KLX250 air box is quite different from the previous generation's air box/boot configuration, with it's large-mouthed flange connection to the air box and larger connecting tube to the carb. Maybe that's where some of the KLX300s extra HP came from


I don't think it's possible to retrofit a KLX300 air box to a 2006 and up bike, but some mods can be made to the sharp cornered entrance way. Too bad, it'd be an interesting comparo.
If I was in the US I'd order a proper sized short velocity stack and afix it to the inside of the air box after removing most of one side of the stack. But from this distance it's too much trouble.
The least I'll do is attach a plate with a nice full radius blending up to the edge of the spigot hole in the flat areas above and below the spigot. Flow bench operators make do with just using a plate with rounded corners (1" radius recommended) attached to cylinder head intake ports so that seems to be the quickest and easiest fix. As does the air filter in the YT AEM video above.
Just take off the rubber boot and put something the same size OD as the spigot ID in there to locate the plate as the JB Weld is setting up and it'd be a quick installation.
Every little bit helps
I did read where a guy made velocity stacks for some other bike out of thin walled plastic plumbing by dipping it into boiling water and forcing it over an upside down shower faucet backing plate or something like that. I can buy 10' of the PVC whatever it is that's the same ID as the spigot for $4, and make a mold out of plaster that has a big fat round curve in it. Then force the hot plastic pipe onto the mold's curves and see what happens.
#4

Well I've started making an insert to smooth out the sharp cornered intersection where the air box body meets the spigot..
Luckily I ordered some tan Alumilite resin mix over a year ago (slow set 7 I think) and finally can put it to use.. It's very lightweight and easy to shape afterwards
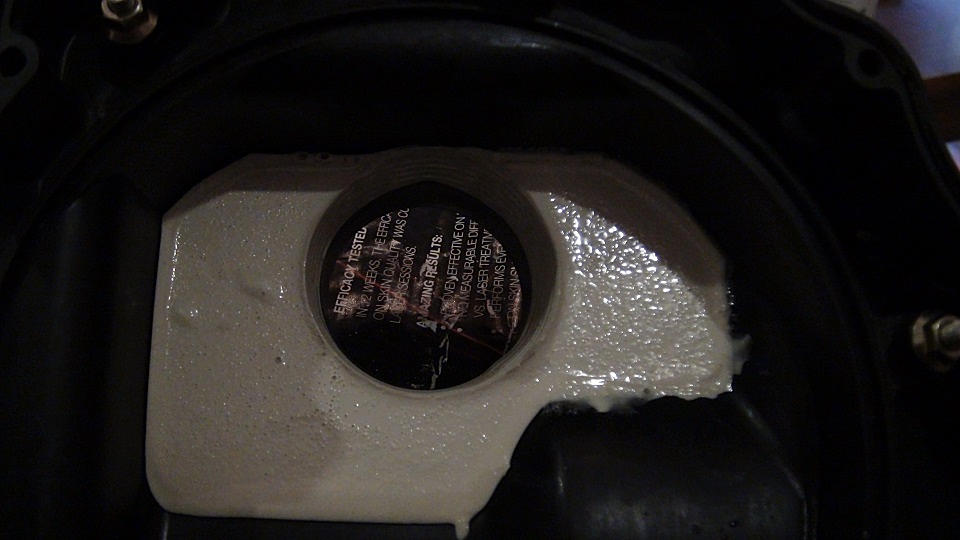
It's only 3/4" thick but it's enough to play with
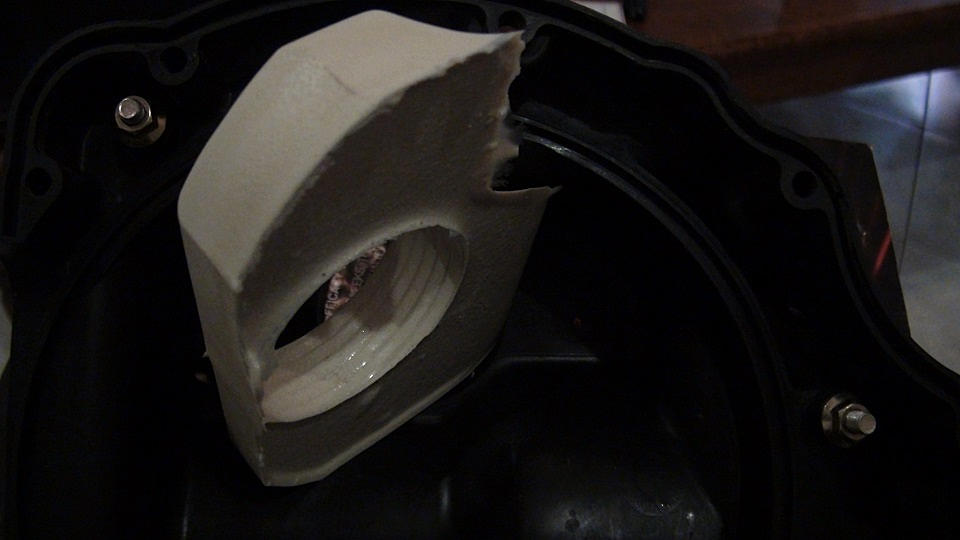
This pic doesn't show it, but the contouring is coming all well...almost like it'd been shaped by water flow
Just a little more and it'll be ready to JB Weld in place. If I get ambitious I may bolt it in instead, but I don't see a reason to go to all that trouble..There shouldn't be a need to take it out again.
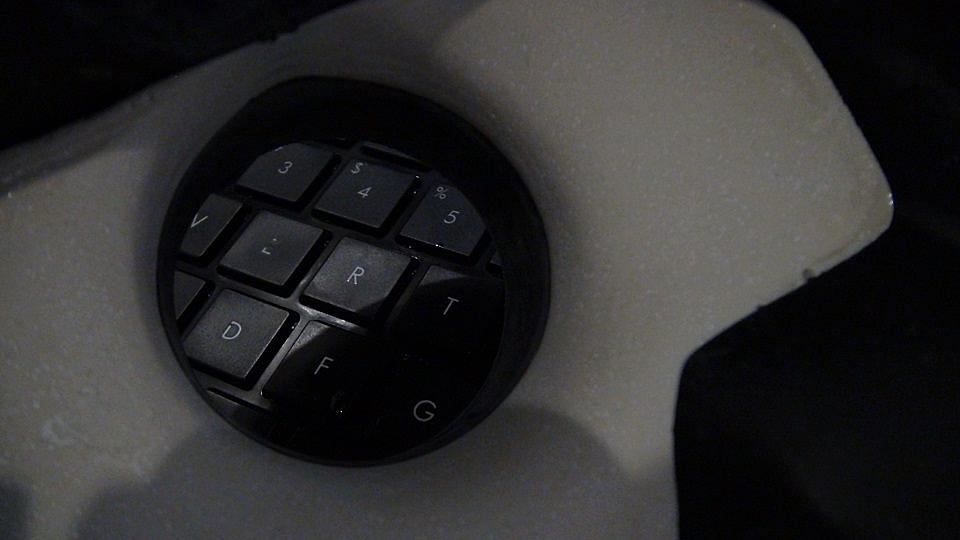
I'm going to try and hold off on installing it until I do some timed runs without it, so I can go back and look for the improvement but...I may just get bored and put it in.
I don't see it making the bike run any worse with it
Luckily I ordered some tan Alumilite resin mix over a year ago (slow set 7 I think) and finally can put it to use.. It's very lightweight and easy to shape afterwards
It's only 3/4" thick but it's enough to play with
This pic doesn't show it, but the contouring is coming all well...almost like it'd been shaped by water flow

I'm going to try and hold off on installing it until I do some timed runs without it, so I can go back and look for the improvement but...I may just get bored and put it in.
I don't see it making the bike run any worse with it

Last edited by Richard Avatar; 07-27-2014 at 05:32 AM.
#6

Well I've been done shaping it, but was thinking I should make another, this time laying down some fiberglass matt then pouring the mix over it. The hardened resin is easy to shape, so I might as well give myself some insurance against catastrophic failure. I dropped it onto cement the other day and it survived just fine, but qn ounce of prevention is better than a lb of cure and all that.
The weather has cleared, and there are mounds of rocks along my dirt road, so the cementing process appears about to happen. Dedicated KLX testing to follow soon.
I did check the a/f ratio on the XR200s idle and it was in the 10s..so I've been going back and forth with that; running the mix screw in which didn't help very much, then reducing pilot jet size from 45 to 42-that helped a little bringing the ratio up to very near 12; next stop will be a 40pj tomorrow just to see what happens.
- Something to do after I pour another batch of mix into the Kawasaki air box front half..
The weather has cleared, and there are mounds of rocks along my dirt road, so the cementing process appears about to happen. Dedicated KLX testing to follow soon.
I did check the a/f ratio on the XR200s idle and it was in the 10s..so I've been going back and forth with that; running the mix screw in which didn't help very much, then reducing pilot jet size from 45 to 42-that helped a little bringing the ratio up to very near 12; next stop will be a 40pj tomorrow just to see what happens.
- Something to do after I pour another batch of mix into the Kawasaki air box front half..
Last edited by Richard Avatar; 08-05-2014 at 07:12 AM.
#8

Oh I think the first one's okay, but I'll be less concerned if I make another with fiberglass at the bottom. Lots of time before I want to put it in anyway.
I read yesterday that 12.8-13.2 is considered best for performance, but mostly I want to make sure it's not way off one way or the other at various throttle settings, and aim for that number if I can.
I read yesterday that 12.8-13.2 is considered best for performance, but mostly I want to make sure it's not way off one way or the other at various throttle settings, and aim for that number if I can.
Last edited by Richard Avatar; 08-05-2014 at 09:47 AM.
#9

While it's easy to understand AFR - 12.8 optimum @ WOT with Dyno loading - Does it follow that 12.8 is optimum at other throttle settings and loadings ? I think I'd want "stoich" at
most steady throttles and light loadings.
most steady throttles and light loadings.
#10

Wiki says:
A stoichiometric mixture unfortunately burns very hot and can damage engine components if the engine is placed under high load at this fuel–air mixture.
Due to the high temperatures at this mixture, detonation of the fuel–air mix shortly after maximum cylinder pressure is possible under high load (referred to as knocking or pinging). Detonation can cause serious engine damage as the uncontrolled burning of the fuel air mix can create very high pressures in the cylinder.
As a consequence, stoichiometric mixtures are only used under light load conditions. For acceleration and high load conditions, a richer mixture (lower air–fuel ratio) is used to produce cooler combustion products and thereby prevent detonation and overheating of the cylinder head.
Since it's possible to have more than a light load at part throttle, I'll be happy just know it's anywhere near 13:1 without too much finessing to get it there. The only risk at that ratio is lesser fuel mileage. FI could provide both lean mix for light loads and richer for performance though.
A stoichiometric mixture unfortunately burns very hot and can damage engine components if the engine is placed under high load at this fuel–air mixture.
Due to the high temperatures at this mixture, detonation of the fuel–air mix shortly after maximum cylinder pressure is possible under high load (referred to as knocking or pinging). Detonation can cause serious engine damage as the uncontrolled burning of the fuel air mix can create very high pressures in the cylinder.
As a consequence, stoichiometric mixtures are only used under light load conditions. For acceleration and high load conditions, a richer mixture (lower air–fuel ratio) is used to produce cooler combustion products and thereby prevent detonation and overheating of the cylinder head.
Since it's possible to have more than a light load at part throttle, I'll be happy just know it's anywhere near 13:1 without too much finessing to get it there. The only risk at that ratio is lesser fuel mileage. FI could provide both lean mix for light loads and richer for performance though.
Last edited by Richard Avatar; 08-05-2014 at 10:39 PM.